Le juste à temps
Jun 15
/
Sébastien Lo Presti
Focus sur le juste à temps, pilier du Lean Management dont l'objectif est de produire : ce que veut le client, au rythme et à la qualité attendus.
Juste à temps ?
Le juste à temps (JAT ou JIT pour Just In Time en anglais) est l’un des piliers du Toyota Production System élaboré dans les années 50 chez Toyota par Taiichi Ohno et Eiji Toyoda.
De la même manière que l’Excellence Opérationnelle désigne à la fois les entreprises les plus performantes dans leur domaine et une démarche permettant de viser l’excellence, le juste à temps présente un double sens qu’il est important d’expliciter.
La mise en place du juste à temps nécessite au préalable de réduire les temps de changement de série, ce qui sera notamment permis par le SMED (Single Minute Exchange of Die).
De la même manière que l’Excellence Opérationnelle désigne à la fois les entreprises les plus performantes dans leur domaine et une démarche permettant de viser l’excellence, le juste à temps présente un double sens qu’il est important d’expliciter.
- Au sens large il correspond à un but, celui de l’excellence en production, résultat d’une élimination permanente des gaspillages. Il subordonne toutes les activités de l’entreprise à la demande client.
- Au sens opérationnel, il consiste à livrer à chaque poste de travail la quantité requise au moment souhaité.
La mise en place du juste à temps nécessite au préalable de réduire les temps de changement de série, ce qui sera notamment permis par le SMED (Single Minute Exchange of Die).
Les avantages du juste à temps
Les avantages liés à la mise en place du juste à temps sont nombreux :
Le juste à temps tend vers une production Make To Order (fabrication à la commande) permettant de limiter au maximum les investissements en stocks. L’enjeux est dès lors d’optimiser le temps de traitement des commandes clients.
- Réduire le temps de traversée des produits, le Lead Time qui correspond au temps nécessaire à la satisfaction d’un besoin client ;
- Limiter les investissements nécessaires notamment via la diminution des stocks et des encours de production ;
- Limiter les gaspillages (on parle de Muda en japonais) ;
- Rendre visibles les problèmes et indispensable leur résolution (Jidoka ou QRQC).
Le juste à temps tend vers une production Make To Order (fabrication à la commande) permettant de limiter au maximum les investissements en stocks. L’enjeux est dès lors d’optimiser le temps de traitement des commandes clients.
Les fondements du juste à temps
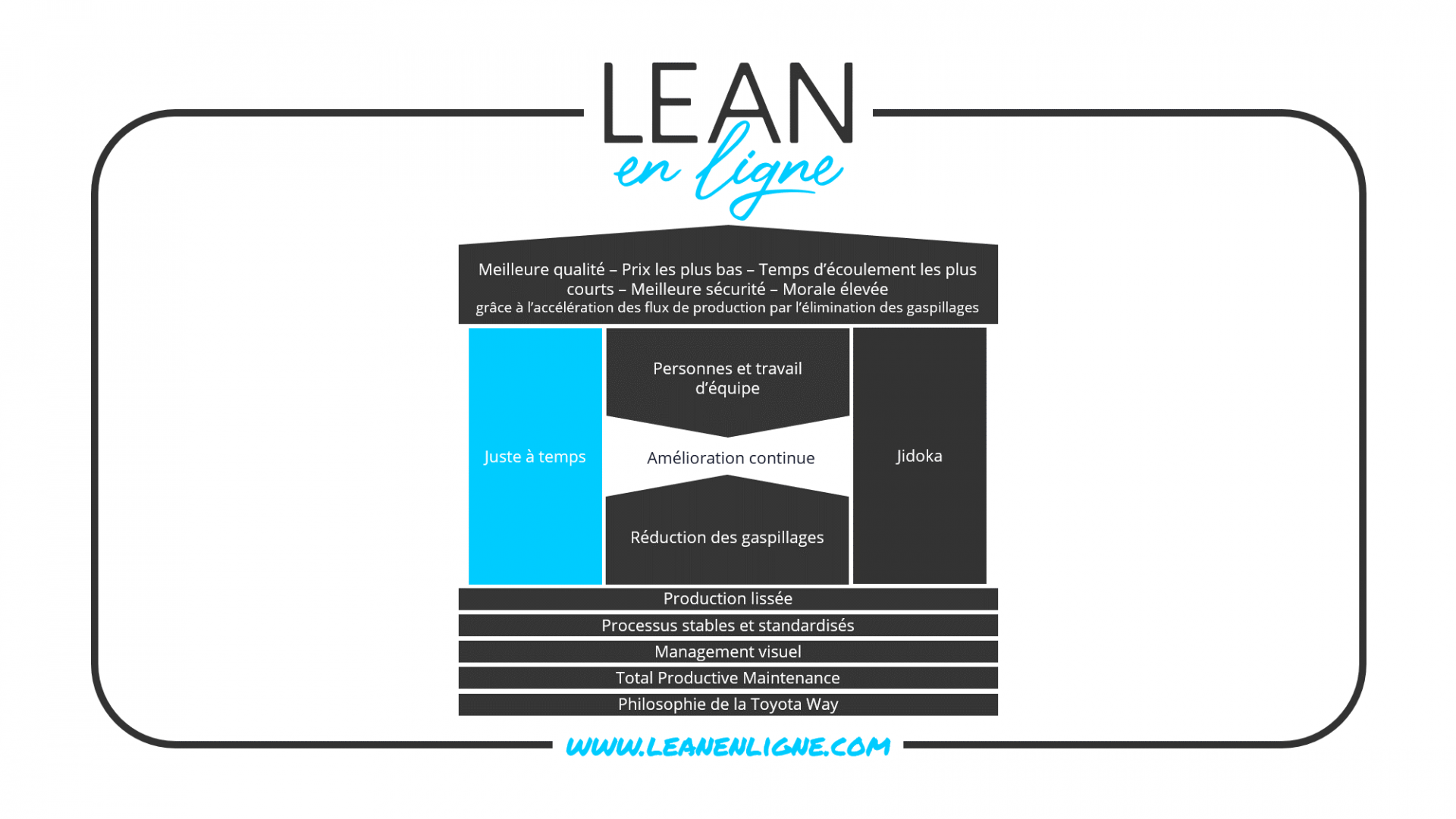
Le JAT (JIT) s’appuie sur plusieurs concepts que nous allons rapidement développer.
D’abord, la réduction de la taille de lot. La réduction de la taille de lot permet de réduire de façon importante le niveau d’en-cours en réduisant ou en supprimant des temps de stockage inter-opérations.
Ensuite, la réduction des temps de changement de série (via le SMED). Le SMED (Single Minute Exchange of Die) est une méthodologie qui permet justement de réduire ces temps de changement de série.
Elle vise des temps de changement d’outil et de réglages quasi instantanés.
Le SMED permet :
Puis, le passage en flux tiré, via le système Kanban. La demande client tire le flux par l’aval, elle est exprimée en fin de processus et déclenche les étapes en amont. Chaque poste envoie un signal de besoin au poste qui est en amont et qui peut alors lancer sa production. Chaque poste produit donc la quantité requise par son client interne quand il en a besoin. Les stocks d’en-cours sont limités et maîtrisés, les problèmes sont révélés.
Enfin, la production lissée (Heijunka) : le Heijunka consiste à découpler les variations de la demande et les possibilités de la production. Pour se faire il faut accumuler les commandes des clients et les organiser de manière à produire chaque jour la même quantité et le même mix de produit : "produire un peu, de tout, tous les jours". Le rythme de production est ainsi stable et régulier.
Le Heijunka permet de se prémunir des Muri et des Mura :
Cette méthode permet de palier les fluctuations de la demande client et éviter ainsi l’alternance de périodes de pics d’activité avec un processus sous-capacitaire et de périodes de sous-charge avec un processus sur-capacitaire.
D’abord, la réduction de la taille de lot. La réduction de la taille de lot permet de réduire de façon importante le niveau d’en-cours en réduisant ou en supprimant des temps de stockage inter-opérations.
Ensuite, la réduction des temps de changement de série (via le SMED). Le SMED (Single Minute Exchange of Die) est une méthodologie qui permet justement de réduire ces temps de changement de série.
Elle vise des temps de changement d’outil et de réglages quasi instantanés.
Le SMED permet :
- D’augmenter la flexibilité des processus dans le cadre de la mise en place d’un flux juste à temps. En effet, la diminution des temps de changement de série permet de baisser la taille des lots de production ;
- D’augmenter la capacité des moyens par la baisse de la durée des arrêts identifiés, impactant favorablement le TRS (Taux de Rendement Synthétique).
Puis, le passage en flux tiré, via le système Kanban. La demande client tire le flux par l’aval, elle est exprimée en fin de processus et déclenche les étapes en amont. Chaque poste envoie un signal de besoin au poste qui est en amont et qui peut alors lancer sa production. Chaque poste produit donc la quantité requise par son client interne quand il en a besoin. Les stocks d’en-cours sont limités et maîtrisés, les problèmes sont révélés.
Enfin, la production lissée (Heijunka) : le Heijunka consiste à découpler les variations de la demande et les possibilités de la production. Pour se faire il faut accumuler les commandes des clients et les organiser de manière à produire chaque jour la même quantité et le même mix de produit : "produire un peu, de tout, tous les jours". Le rythme de production est ainsi stable et régulier.
Le Heijunka permet de se prémunir des Muri et des Mura :
- Les Muri représentent une charge de travail excessive pour les hommes et machines, qui consiste à pousser une machine ou un homme au-delà de ses limites. Les pics d’activité en sont un très bon exemple ;
- Les Muras représentent la variabilité c’est à dire des variations qui conduisent à une situation déséquilibrée. Une hausse très importante de la demande client dans le cas qui nous concerne.
Cette méthode permet de palier les fluctuations de la demande client et éviter ainsi l’alternance de périodes de pics d’activité avec un processus sous-capacitaire et de périodes de sous-charge avec un processus sur-capacitaire.
Vous avez apprécié cet article ? Faites-le savoir !
À propos de l'auteur
Passionné par les sciences sociales, la gestion de projet et le management de la qualité.
Animé par la volonté de partager et de transmettre des connaissances.
Je suis par ailleurs cofondateur de Lean en ligne, organisme de formation spécialisé en Excellence Opérationnelle.
Le blog de Lean en ligne - derniers articles publiés
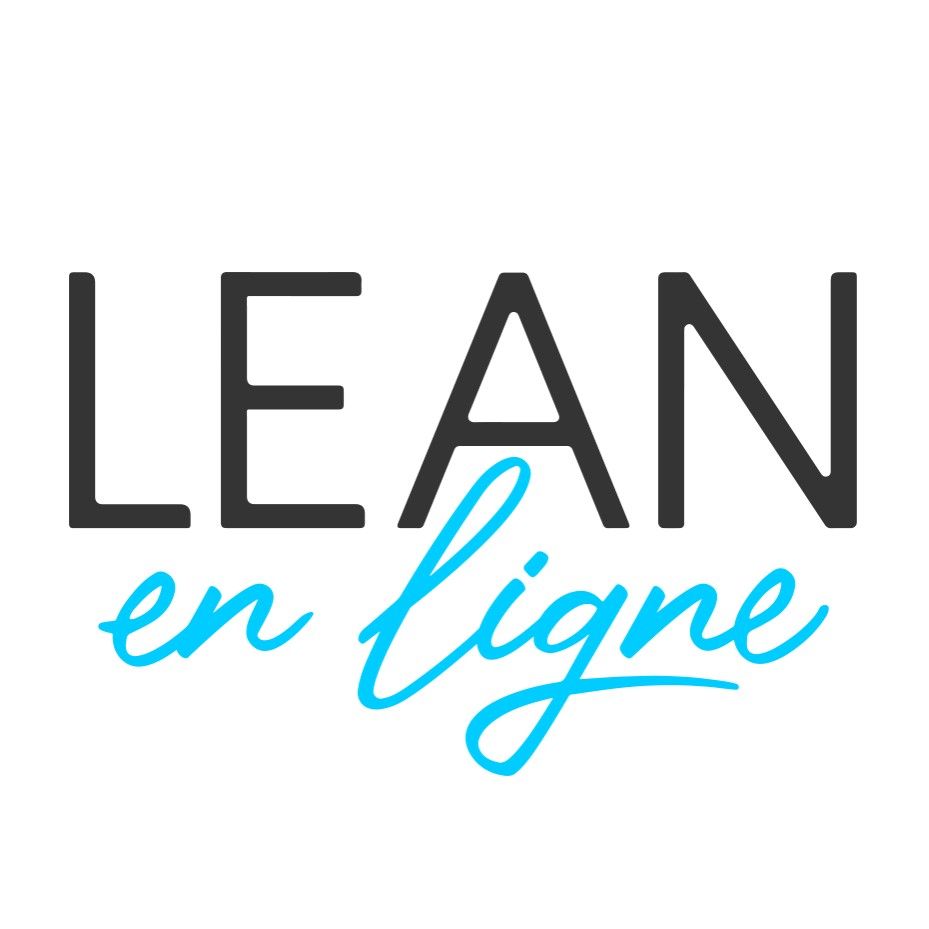
-
Lean en ligne - Sigmatic SAS
-
30 Boulevard de Sébastopol, 75004 Paris
-
+33 6 89 33 95 76
Suivre l'actualité de Lean en ligne
Merci et à bientôt !
Nos offres
Formations à la une
Ressources gratuites
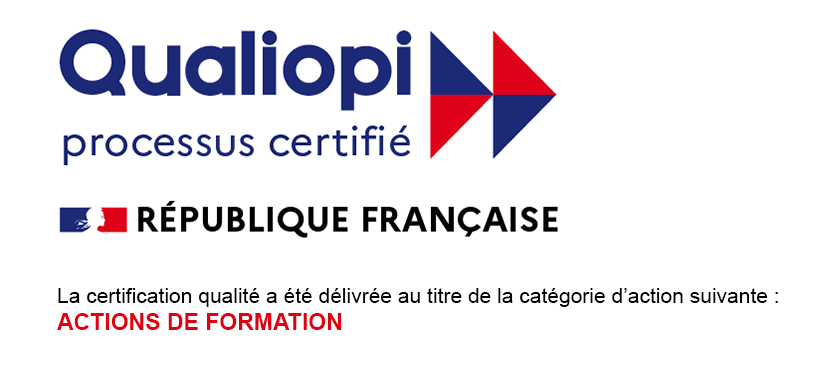
Organisme de Formation enregistré sous le numéro 11756146475. Cet enregistrement ne vaut pas agrément de l’État
Write your awesome label here.
On reste en contact ?
Merci à bientôt !