Kanban, origines et fondements
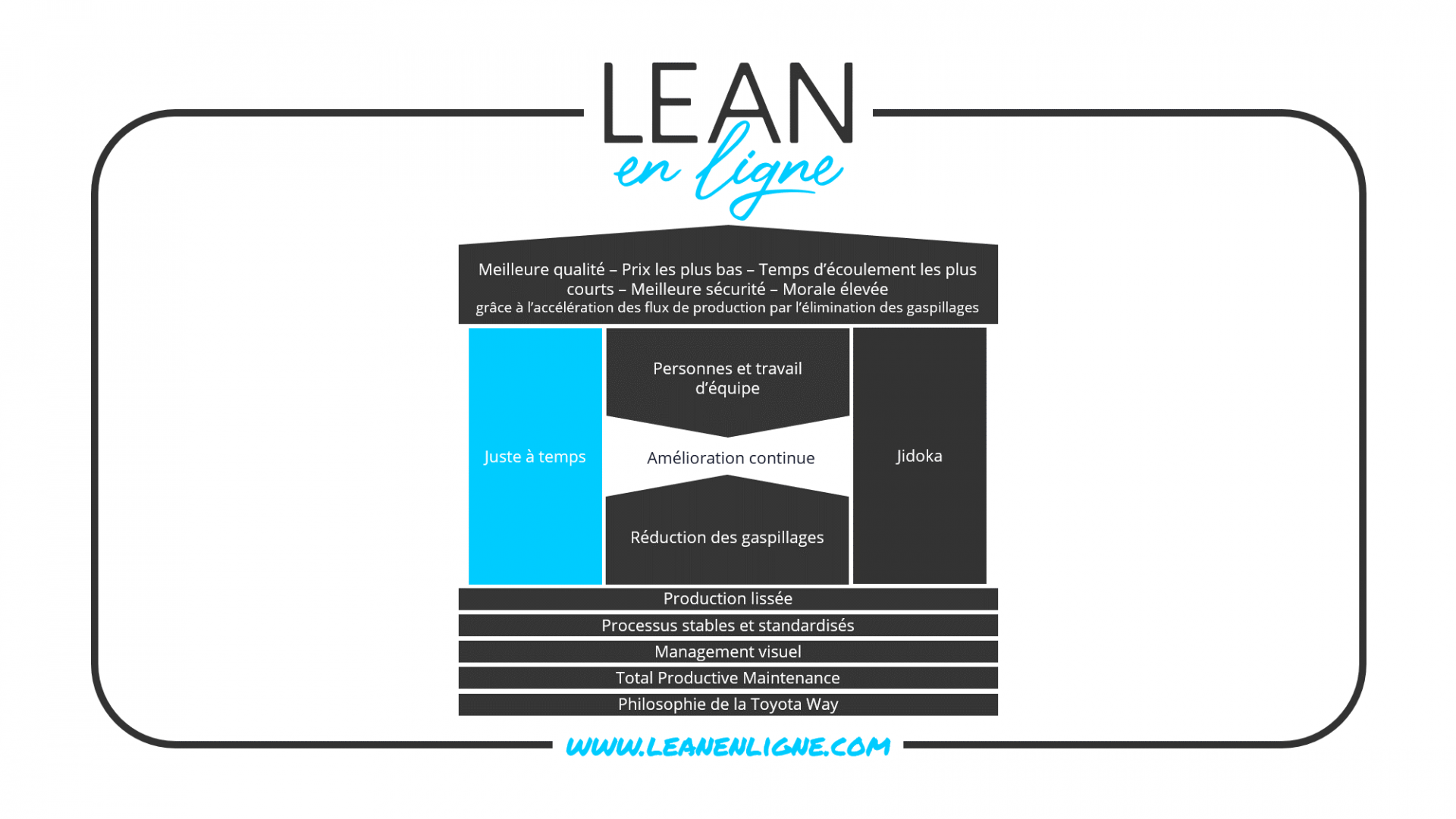
Kanban un principe simple basé sur des étiquettes
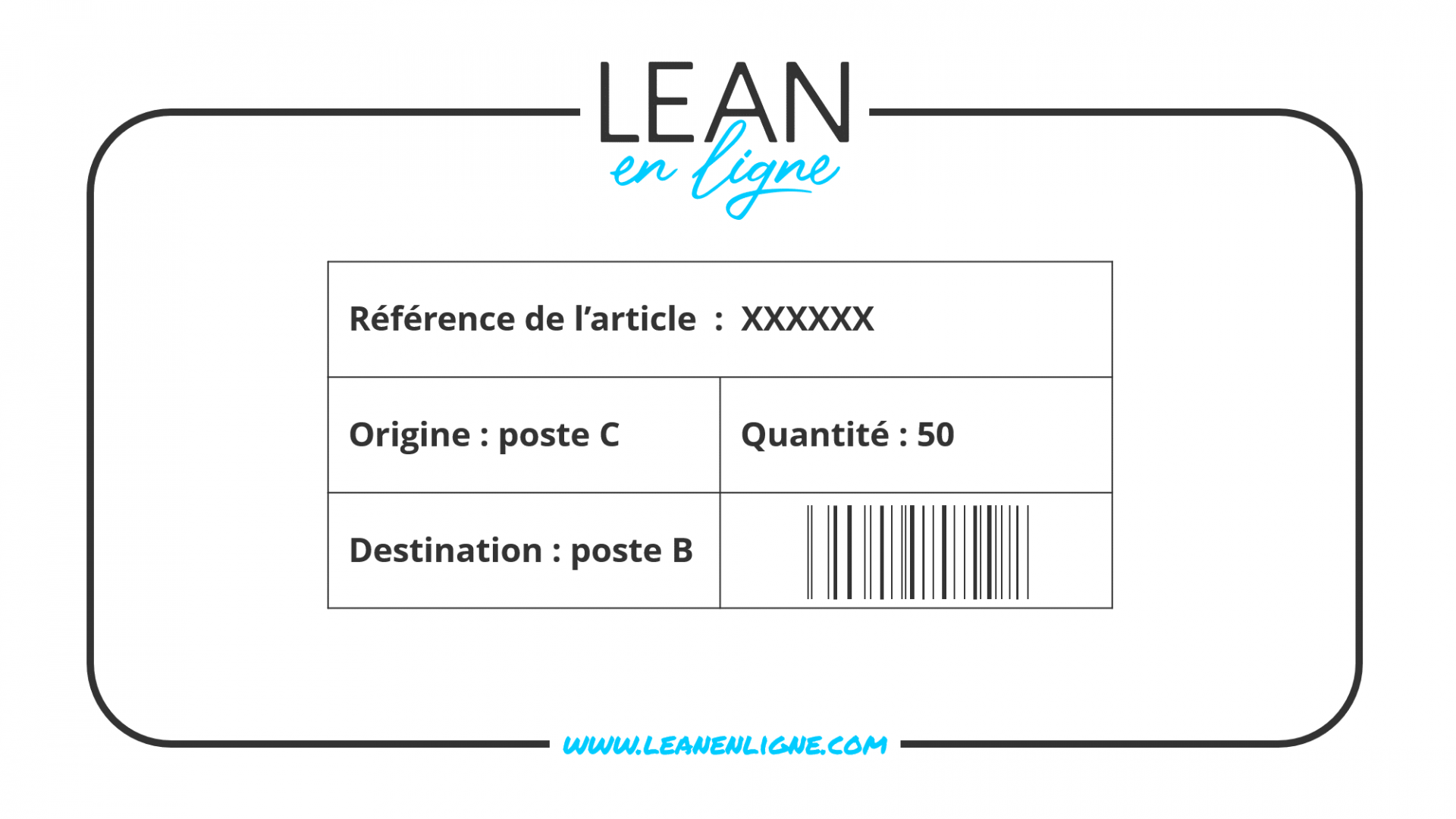
Kanban, une illustration pratique
On constate que ceux-ci vont remonter le flux physique pour générer des productions et des réapprovisionnements.
Partons du poste 3. Celui-ci dispose d’un petit stock de pièces. Lorsqu’il commence à consommer les pièces, il va détacher l’étiquette Kanban associée aux pièces et la renvoyer à son fournisseur (Poste 2).
Le Poste 2 dispose ainsi de toutes les informations (pièces et quantités à transmettre) lui permettant de réapprovisionner son client, le Poste 3.
Si le Poste 2 est un poste de fabrication, il va à son tour lancer la fabrication de nouvelles pièces pour répondre au Kanban reçu. Pour ce faire il va utiliser des composants et ainsi renvoyer l’étiquette associée à ceux-ci au Poste 1.
Le Kanban est le moyen simple par lequel le signal de réapprovisionnement est envoyé de l’aval vers l’amont.
Pas de consommation de pièces du Poste 3 (par exemple) ; pas d’envoi de Kanban. Ce système est très simple, et auto-adaptatif.
Dans la seconde partie de cette article, nous allons détailler la méthode permettant de calculer le nombre de Kanbans nécessaires dans une boucle.
Partons du poste 3. Celui-ci dispose d’un petit stock de pièces. Lorsqu’il commence à consommer les pièces, il va détacher l’étiquette Kanban associée aux pièces et la renvoyer à son fournisseur (Poste 2).
Le Poste 2 dispose ainsi de toutes les informations (pièces et quantités à transmettre) lui permettant de réapprovisionner son client, le Poste 3.
Si le Poste 2 est un poste de fabrication, il va à son tour lancer la fabrication de nouvelles pièces pour répondre au Kanban reçu. Pour ce faire il va utiliser des composants et ainsi renvoyer l’étiquette associée à ceux-ci au Poste 1.
Le Kanban est le moyen simple par lequel le signal de réapprovisionnement est envoyé de l’aval vers l’amont.
Pas de consommation de pièces du Poste 3 (par exemple) ; pas d’envoi de Kanban. Ce système est très simple, et auto-adaptatif.
Dans la seconde partie de cette article, nous allons détailler la méthode permettant de calculer le nombre de Kanbans nécessaires dans une boucle.
Certification Green Belt
à partir de 249€
Calculer le besoin en Kanban dans une boucle
Le nombre d’étiquettes à mettre dans une boucle Kanban correspond à la consommation du client durant le délai de réapprovisionnement.
Posons :
Une demande client de 12 conteneurs par jours ;
Des équipes travaillant 8 heures par jour ;
Un délai de réapprovisionnement de 2 heures.
Nous aurons alors :
Soit besoin de 3 Kanban à positionner dans la boucle Kanban.
On aura ainsi un cycle continu dans lequel il n’y a pas de rupture. Trois Kanban circuleront en permanence dans la boucle.
Dans la pratique on rencontre souvent des systèmes de Kanban dits à deux boucles (notamment lorsqu’il y a plusieurs clients pour une référence donnée).
Dans ce cas, il y a deux types de Kanban :
Les Kanban de fabrication (ou de production) circulent entre :
Les Kanban de transfert (ou de prélèvement) circulent entre :
Posons :
Une demande client de 12 conteneurs par jours ;
Des équipes travaillant 8 heures par jour ;
Un délai de réapprovisionnement de 2 heures.
Nous aurons alors :
- D = 12 ;
- C = 0,25 (2/8) ;
- D*C = 3
Soit besoin de 3 Kanban à positionner dans la boucle Kanban.
On aura ainsi un cycle continu dans lequel il n’y a pas de rupture. Trois Kanban circuleront en permanence dans la boucle.
Dans la pratique on rencontre souvent des systèmes de Kanban dits à deux boucles (notamment lorsqu’il y a plusieurs clients pour une référence donnée).
Dans ce cas, il y a deux types de Kanban :
- Le Kanban de production ou de fabrication (Production Kanban) ;
- Le Kanban de transfert ou de prélèvement (Whithdrawal Kanban) ;
Les Kanban de fabrication (ou de production) circulent entre :
- Le centre de production ;
- Le magasin de stockage situé en aval de ce centre.
Les Kanban de transfert (ou de prélèvement) circulent entre :
- Le magasin de stockage ;
- Les centres de consommation de la référence.
Le tableau multi-kanban
La ligne verte représente le seuil de lancement de la production pour un produit donné. Tant que le nombre d’étiquettes n’atteint pas ce seuil, la production correspondant à cette référence n’est pas lancée. Ainsi, dans notre exemple, la production ne sera pas lancée pour le produit Z. En revanche, les productions de X et Y peuvent être lancées.
La ligne rouge constitue quant à elle un seuil d’alerte. Quand le nombre de Kanban cumulés atteint cette ligne, cela signifie qu’il faut absolument lancer la fabrication de nouvelles pièces sans quoi le magasin ou le client risque de se trouver en situation de rupture.
Dans notre exemple, il est impératif de lancer une production pour Y.
Le tableau multi-kanban permet ainsi de prioriser les demandes et de les traiter au moment le plus opportun.
Dans les usines, ont souvent été mis en place des « petits trains d’approvisionnement ». Selon un schéma prédéterminé, un opérateur fait alors le tour des postes de l’usine à fréquences régulières , il prélève les cartes Kanban, et revient au magasin. Prélève les composants nécessaires et réapprovisionne les différents postes de travail.
La ligne rouge constitue quant à elle un seuil d’alerte. Quand le nombre de Kanban cumulés atteint cette ligne, cela signifie qu’il faut absolument lancer la fabrication de nouvelles pièces sans quoi le magasin ou le client risque de se trouver en situation de rupture.
Dans notre exemple, il est impératif de lancer une production pour Y.
Le tableau multi-kanban permet ainsi de prioriser les demandes et de les traiter au moment le plus opportun.
Dans les usines, ont souvent été mis en place des « petits trains d’approvisionnement ». Selon un schéma prédéterminé, un opérateur fait alors le tour des postes de l’usine à fréquences régulières , il prélève les cartes Kanban, et revient au magasin. Prélève les composants nécessaires et réapprovisionne les différents postes de travail.
Kanban et projet Lean Six Sigma DMAIC
Dans un projet Lean Six Sigma DMAIC, le déploiement d’un système Kanban pourra être assuré par un chef de projet Green Belt (ou Black Belt) dans le cadre de la mise en place du juste à temps soit en phase I pour Améliorer ou Improve.
Pour rappel, les objectifs de la phase I d'un projet DMAIC sont les suivants :
Pour rappel, les objectifs de la phase I d'un projet DMAIC sont les suivants :
- Générer des solutions pour adresser les causes racines des problèmes identifiés en phase A (Analyse ou Analyser) ;
- Sélectionner les solutions les plus pertinentes et les tester ;
- Organiser la mise en œuvre des solutions retenues.
À propos de l'auteur
Passionné par les sciences sociales, la gestion de projet et le management de la qualité.
Animé par la volonté de partager et de transmettre des connaissances.
Je suis par ailleurs cofondateur de Lean en ligne, organisme de formation spécialisé en Excellence Opérationnelle.