Projet Lean Six Sigma - Exemple
Apr 8
/
Béryl Mereaux
Découvrez dans cet article le retour d'expérience de Béryl, Black Belt, à propos de son tout premier projet Lean Six Sigma.
Béryl reviendra sur les caractéristiques du projet, sur ce qu'elle en a appris à propos du processus et de la méthodologie.
Bonne lecture !
Béryl reviendra sur les caractéristiques du projet, sur ce qu'elle en a appris à propos du processus et de la méthodologie.
Bonne lecture !
Un projet Lean Six Sigma aux multiples facettes
Certaines expériences nous apportent
plus que d'autres. Et parfois il faut regarder 2, 3, 10 fois en arrière pour se
remémorer le fil de son histoire et trouver de nouvelles lumières dans son
propre vécu.
Le premier projet que j'ai mené, m'a éclairé une bonne dizaine de fois sur des notions de performance, de 80-20 ou encore sur les relations humaines. C’est un des projets dont j’ai décortiqué le déroulement maintes fois pour avancer dans chacune de mes expériences en Lean Six Sigma.
C’était il y a 20 ans. Il s'agissait de mon premier travail, en tant qu'ingénieure de recherche. Autant bien cerner le personnage de l'époque : je voulais découvrir, tester et inventer.
En plus de mes objectifs purement axés recherche, j'avais pour objectif de décrocher ma Green Belt. Il me fallait donc identifier un projet éloigné de celui de mes objectifs principaux. Je travaillais à cette époque sur un site de production et d'assemblage de biens d'équipements. Les possibilités de projets étaient multiples.
Sur un des équipements assemblés, une cartouche d'imprimante laser, une étape de fabrication consistait à déposer une poudre lubrifiante sur un balai en caoutchouc. Ce dépôt était réalisé au moyen d'un fluide s'évaporant après le dépôt de la poudre. Le balai avait une fonction très importante dans la cartouche : c'est lui qui permettait de retirer l'excès de toner sur le cylindre de la cartouche d’imprimante une fois la feuille imprimée. La poudre permettait de réduire le frottement entre le balai et le cylindre de la cartouche d’imprimante, optimisant ainsi la fonction et la durée de vie du balai.
Le fluide utilisé était amené à être remplacé car le fournisseur était contraint par la réglementation d'arrêter de le produire. Ce fluide émettait des gaz à effet de serre. Bien sûr les cadences de production devaient être maintenues pour permettre à l'entreprise de maintenir sa position dans un secteur très concurrentiel. Le nouveau fluide était déjà identifié.
Voilà un projet simple et donc parfait pour une ingénieure débutante, qui pouvait démarrer sans inquiétude.
Le premier projet que j'ai mené, m'a éclairé une bonne dizaine de fois sur des notions de performance, de 80-20 ou encore sur les relations humaines. C’est un des projets dont j’ai décortiqué le déroulement maintes fois pour avancer dans chacune de mes expériences en Lean Six Sigma.
C’était il y a 20 ans. Il s'agissait de mon premier travail, en tant qu'ingénieure de recherche. Autant bien cerner le personnage de l'époque : je voulais découvrir, tester et inventer.
En plus de mes objectifs purement axés recherche, j'avais pour objectif de décrocher ma Green Belt. Il me fallait donc identifier un projet éloigné de celui de mes objectifs principaux. Je travaillais à cette époque sur un site de production et d'assemblage de biens d'équipements. Les possibilités de projets étaient multiples.
Sur un des équipements assemblés, une cartouche d'imprimante laser, une étape de fabrication consistait à déposer une poudre lubrifiante sur un balai en caoutchouc. Ce dépôt était réalisé au moyen d'un fluide s'évaporant après le dépôt de la poudre. Le balai avait une fonction très importante dans la cartouche : c'est lui qui permettait de retirer l'excès de toner sur le cylindre de la cartouche d’imprimante une fois la feuille imprimée. La poudre permettait de réduire le frottement entre le balai et le cylindre de la cartouche d’imprimante, optimisant ainsi la fonction et la durée de vie du balai.
Le fluide utilisé était amené à être remplacé car le fournisseur était contraint par la réglementation d'arrêter de le produire. Ce fluide émettait des gaz à effet de serre. Bien sûr les cadences de production devaient être maintenues pour permettre à l'entreprise de maintenir sa position dans un secteur très concurrentiel. Le nouveau fluide était déjà identifié.
Voilà un projet simple et donc parfait pour une ingénieure débutante, qui pouvait démarrer sans inquiétude.
Apprentissages sur le processus et la méthodologie
La machine de production déposant la
poudre lubrifiante fut mise à disposition. Les équipes méthode et production participèrent
au projet. Leur participation consista à me fournir une aide si nécessaire. En
fait j’étais très autonome et seule.
Très vite j’ai constaté que le procédé de dépôt était en place, mais les connaissances des caractéristiques clefs du procédé étaient faibles. Par exemple, la quantité de poudre lubrifiante nécessaire n'avait jamais été optimisée pour avoir un produit final plus performant. Un temps de déposition rapide était nécessaire pour éviter que le fluide ne s'évapore trop vite, ce temps n'avait jamais été ajusté. Par ailleurs d'autres facteurs influents comme l'inclinaison du support en caoutchouc, sa nuance matière, le dimensionnement du balai, la vitesse de mélange poudre/fluide n'avaient jamais été étudiés.
C'était passionnant, il y avait de la chimie, de la tribologie et même du logiciel ! Et j'ai foncé dans une multitude d'expériences coachée par une black belt de l’entreprise.
Le fluide fut remplacé avec succès sans impact sur la qualité des produits. Mais ce n'est pas le résultat que je retiens.
Évidemment il y eut des problèmes dont j’ai pu tirer quelques leçons utiles :
Ce sont mes principaux apprentissages.
Très vite j’ai constaté que le procédé de dépôt était en place, mais les connaissances des caractéristiques clefs du procédé étaient faibles. Par exemple, la quantité de poudre lubrifiante nécessaire n'avait jamais été optimisée pour avoir un produit final plus performant. Un temps de déposition rapide était nécessaire pour éviter que le fluide ne s'évapore trop vite, ce temps n'avait jamais été ajusté. Par ailleurs d'autres facteurs influents comme l'inclinaison du support en caoutchouc, sa nuance matière, le dimensionnement du balai, la vitesse de mélange poudre/fluide n'avaient jamais été étudiés.
C'était passionnant, il y avait de la chimie, de la tribologie et même du logiciel ! Et j'ai foncé dans une multitude d'expériences coachée par une black belt de l’entreprise.
Le fluide fut remplacé avec succès sans impact sur la qualité des produits. Mais ce n'est pas le résultat que je retiens.
Évidemment il y eut des problèmes dont j’ai pu tirer quelques leçons utiles :
- Afin de déterminer la quantité de poudre nécessaire, j'avais commencé par
peser les balais avec et sans dépôt. Mais l’étude de répétabilité et
reproductibilité révéla que ce moyen de contrôle n'était pas déterminant.
Ce fut une première leçon pour moi et mes collègues qui pensaient que ce serait
un projet facile. Il a fallu faire un « brainstorming », observer et
trouver d'autres moyens pour caractériser ce dépôt. J’ai passé de nombreuses
heures en laboratoire à étudier la viscosité du mélange, mais aussi sur la
ligne production à chronométrer la machine de dépose. Le temps passé sur le
projet était conséquent et ce dès la phase Mesure.
- Lors de la phase de tests de la solution, j‘ai été confronté à des pertes
de données. Il a fallu que je retrousse mes manches et que j’écrive un code
pour enregistrer les valeurs automatiquement afin de les envoyer dans une autre
entité située en Angleterre. Le temps que je passais sur ce projet devenait critique
vis-à-vis de ma mission principale. Mais j’appris à m’organiser pour être plus efficace
en compartimentant mon agenda.
- Lors de la mise en place de la solution finale, j’étais fière de mes
calculs, et de tous ces essais réalisés. Comme j’avais déjà passé beaucoup de
temps sur ce projet et que c’était un projet « simple » à objectif
environnemental, il fut décidé de ne pas faire de phase pilote. Quelques
semaines après la mise en place de cette solution, le taux de retour client fut
phénoménal… Nous étions passé de 2 retours semaine à plus de 20… Evidemment je
fus convoquée par le responsable de production, personne n’avait suivi le
projet, personne ne connaissait la machine. Il fallait que je résolve très vite
le problème. Dans ce type de situation, le cerveau se met rapidement en route
et mon erreur me sauta aux yeux. Je n’avais pris aucune marge, mes courbes de
tests se croisaient en un point et c’est à cette intersection que j’avais établi
la concentration à utiliser en production. Evidemment j’ai vite corrigé
l’erreur, puis le responsable méthode m’a aidé pour faire un petit pilote qui
fut concluant.
- Au moment de la clôture du projet, soit un mois après ce pilote, j’avais déjà beaucoup appris. Et c’est à ce moment-là qu’à nouveau le nombre de retours client se remit à frémir… Arrêt de la ligne, vérification des paramètres, analyse causale reprise de A à Z… et je compris en voyant un chariot plein de balais déjà couverts de poudre lubrifiante dans l’atelier…. Le seul opérateur de la ligne avait fait un petit stock pour pouvoir temporiser sa production. Mais le stock qu’il avait constitué correspondait à des balais de tests, non prévus pour être installés sur les machines. Ce fut le moment le plus difficile du projet, car je me suis rendue compte que je n’avais pas assez impliqué cet opérateur. Alors j’avais mes excuses, nous ne parlions pas la même langue, on ne l’avait pas intégré dans l’équipe projet. Mais surtout je n’avais pris en compte l’impact de ce projet dans l’organisation de la ligne et surtout dans le travail de cet opérateur qui devait réaliser un certain quota chaque jour. Il avait participé aux essais en rognant sur ses quotas. Alors dès qu’il le pouvait, il avait mis des produits de côté.
Ce sont mes principaux apprentissages.
Enseignements personnels
J’ai aussi eu des victoires personnelles que je
qualifierai de « discrètes » :
Pour conclure :
Lorsqu’un projet Lean et Six Sigma est démarré, il est primordial d'avoir une vision d'ensemble des processus impactés. Dans ce projet, si j'avais uniquement étudié l'opération de dépôt, j'aurai omis quelques paramètres essentiels.
Par ailleurs, rappelons que le Lean et le Six Sigma sont étroitement liés. En effet mettre en place une solution sans regarder l’impact organisationnel ou l’impact en terme qualité peut s’avérer coûteux.
Enfin l’humain est essentiel, j’enfonce une porte en l’écrivant. Ce n’est pas si simple de jauger le bon niveau d’implication des acteurs d’un projet, en revanche il est souvent possible en cours de projet de faire un pas en arrière, d’expliquer, et prendre le temps pour que la solution du projet soit celle qui atteigne le meilleur compromis.
- L’objectif
du projet consistait uniquement en un objectif environnemental. La fiabilité du dépôt n'était pas un objectif projet
initial mais nous avons réussi à éliminer tout défaut chez les clients finaux.
La courbe des retours resta à 0 ! Ce fut un soulagement de savoir nos
clients satisfaits.
- Le nouveau
produit coûtait plus cher. Cependant,
en étudiant précisément la machine de dépose du lubrifiant, j'ai pu optimiser les quantités utilisées mais aussi les
temps d'application du lubrifiant, ce qui a permis d'absorber les coûts
supplémentaires de la matière première, mais aussi de faire quelques économies.
Cela correspondait à mon salaire annuel. Depuis je me suis toujours dit
qu’il ne fallait pas se limiter dans les objectifs secondaires et au moins
essayer.
- J’ai bien sûr acquis une expertise au sein de l’entreprise. Nous maîtrisions mieux cette étape de la production. Tout ceci me permit de gagner en confiance.
Pour conclure :
Lorsqu’un projet Lean et Six Sigma est démarré, il est primordial d'avoir une vision d'ensemble des processus impactés. Dans ce projet, si j'avais uniquement étudié l'opération de dépôt, j'aurai omis quelques paramètres essentiels.
Par ailleurs, rappelons que le Lean et le Six Sigma sont étroitement liés. En effet mettre en place une solution sans regarder l’impact organisationnel ou l’impact en terme qualité peut s’avérer coûteux.
Enfin l’humain est essentiel, j’enfonce une porte en l’écrivant. Ce n’est pas si simple de jauger le bon niveau d’implication des acteurs d’un projet, en revanche il est souvent possible en cours de projet de faire un pas en arrière, d’expliquer, et prendre le temps pour que la solution du projet soit celle qui atteigne le meilleur compromis.
Vous avez apprécié cet article ? Faites-le savoir !
Le blog de Lean en ligne - derniers articles publiés
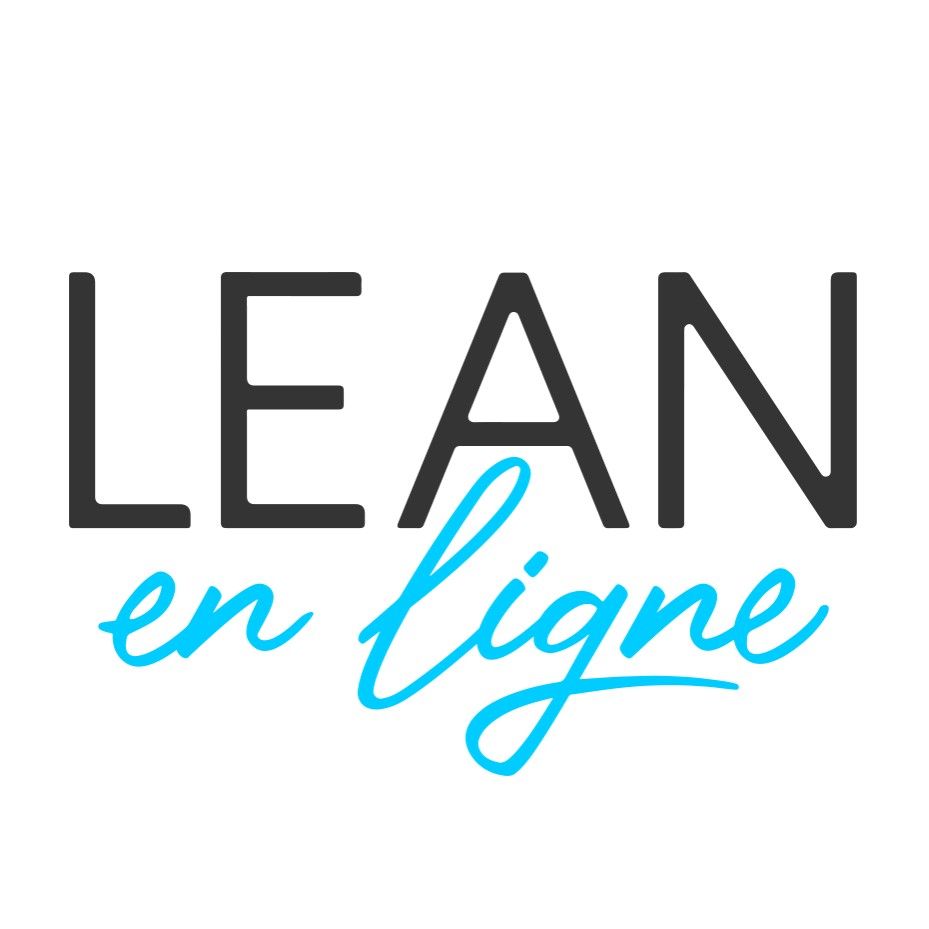
-
Lean en ligne - Sigmatic SAS
-
30 Boulevard de Sébastopol, 75004 Paris
-
+33 6 89 33 95 76
Suivre l'actualité de Lean en ligne
Merci et à bientôt !
Nos offres
Formations à la une
Ressources gratuites
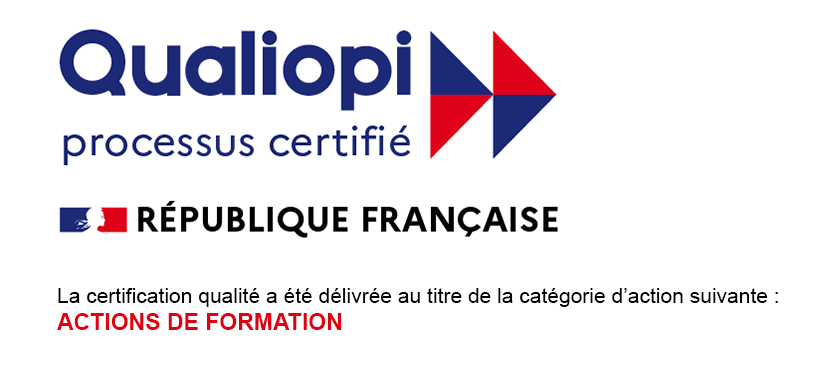
Organisme de Formation enregistré sous le numéro 11756146475. Cet enregistrement ne vaut pas agrément de l’État
Write your awesome label here.
On reste en contact ?
Merci à bientôt !