Standardisation : la base de l'amélioration continue
3 types de standards
Standards : quels intérêts ?
Certification Green Belt
à partir de 249€
Standards et management visuel
La formalisation de standards s’appuie généralement sur du management visuel. Le management visuel consiste à diriger avec les yeux afin de :
Le management visuel, c’est l’information qui va être accessible à tous et très lisible.
Le principal intérêt du management visuel réside précisément dans cette information décentralisée, facile et intuitive à comprendre. Étant gérée par les opérationnels, elle permet :
Le management visuel constitue une façon de manager la performance. Il passe par :
- Rendre visuel le fonctionnement nominal (le standard) ;
- Rendre visible en temps réel tout écart au standard ;
- Rendre toutes les informations importantes visibles de tous ;
- Afficher clairement les problèmes pour qu’ils soient traités, et non mis sous le tapis, avec le plus de réactivité et d’efficacité possibles ;
- Afficher des indicateurs de performance (KPI pour Key Performance Indicator).
Le management visuel, c’est l’information qui va être accessible à tous et très lisible.
Le principal intérêt du management visuel réside précisément dans cette information décentralisée, facile et intuitive à comprendre. Étant gérée par les opérationnels, elle permet :
- D’impliquer collectivement les équipes ;
- De les responsabiliser ;
- De contribuer à la motivation des équipes qui vont être impliquées également dans la résolution des dysfonctionnements qu’elles ont les moyens d'identifier.
Le management visuel constitue une façon de manager la performance. Il passe par :
- La mise à jour régulière des données ;
- La mise à disposition d’informations concernant le déroulement des processus ;
- Le marquage et le repérage des sources de danger, des valeurs de référence et des standards.
4 illustrations de management visuel
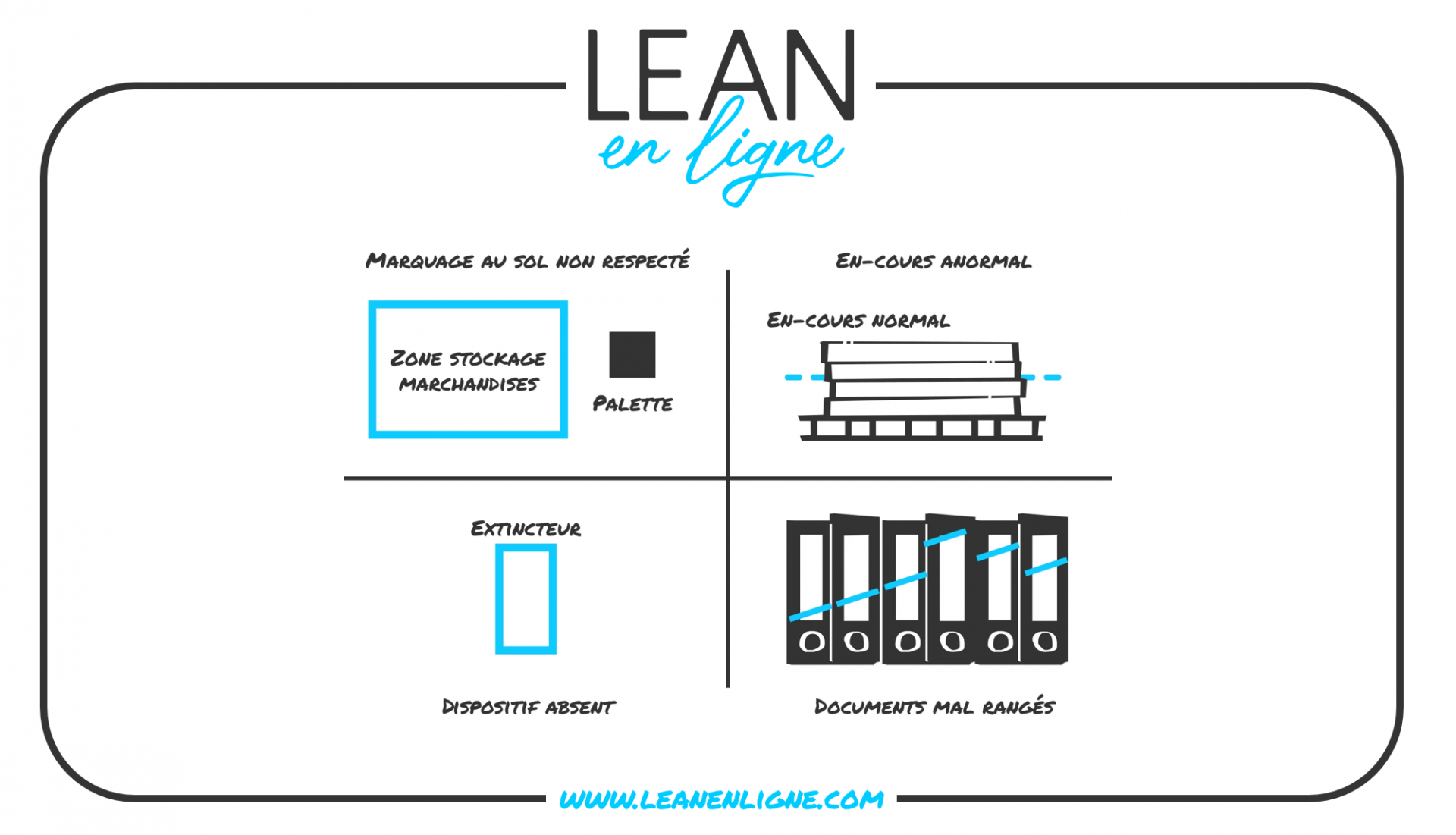
Standardisation et projets Lean Six Sigma DMAIC
Standards et management visuel seront notamment utilisés par un chef de projet Green Belt (ou Black Belt) en phase C (pour Maîtriser ou Control) d'un projet Lean Six Sigma DMAIC, lorsqu’il s’agira de :
- Généraliser les solutions éprouvées lors de la phase pilote ;
- De capitaliser les enseignements acquis sur le processus et d'assurer la pérennité des résultats obtenus.
À propos de l'auteur
Passionné par les sciences sociales, la gestion de projet et le management de la qualité.
Animé par la volonté de partager et de transmettre des connaissances.
Je suis par ailleurs cofondateur de Lean en ligne, organisme de formation spécialisé en Excellence Opérationnelle.