Valoriser les gaspillages
Cet article s'intéresse aux enjeux liés à la valorisation financière des gaspillages et fournit des exemples de calculs.
Bonne lecture
Pourquoi valoriser les gaspillages ?
Il existe 7 types de gaspillages observables sur le terrain :
- Déplacements et mouvements inutiles,
- Surproduction,
- Attentes,
- Surstokage et stocks inutiles,
- Transports,
- Rebuts et retouches,
- Étapes superflues.
Nous l'avons présenté dans l'article "Pourquoi déployer le Lean ?", les coûts de production peuvent être diminués en réduisant les taux de rebuts et de retouches et plus globalement par la recherche puis l'élimination des gaspillages.
Valoriser les gaspillages permet de quantifier leur impact financier et ainsi :
- d'évaluer le retour sur investissement des initiatives potentielles,
- de prioriser les actions de progrès à mener,
- de communiquer à propos des gains obtenus.
Comment mesurer les gaspillages ?
- Gemba Walk. Le Gemba Walk consiste à se rendre sur le terrain où la valeur ajoutée est créée pour observer en temps réel où se produisent les gaspillages. Des interviews peuvent également être menées avec les acteurs du processus en pratiquant l'écoute active.
- Cartographie des processus. La cartographie de la chaîne de valeur permet d'identifier les étapes du processus et de visualiser où les gaspillages se produisent. Les cartographies de processus peuvent être alimentées par des mesures spécifiques pour aller plus loin.
- Observations à temps constant et à temps continu. Ces observations permettent de quantifier de manière factuelle la part de temps associée à des gaspillages.
- Analyse des stocks. Ce type d'analyse peut être intitié par une extraction et une analyse des données de l'ERP.
- Analyse des défauts et retouches. Ce type d'analyse peut être réalisé à partir des données de l'assurance qualité ou des informations extraites de l'ERP.
- Innovation participative. Les systèmes de suggestions permettent également d'évaluer les gapillages à partir des remontées terrain.
Comment valoriser les gaspillages ?
Exemples de calculs
- Coût du temps perdu : le temps passé à réaliser des mouvements inutiles constitue du temps non productif.
- Coût ergonomique : les mouvements inutiles peuvent causer de la fatigue, des accidents ou des maladies professionnelles, augmentant les coûts liés aux arrêts de travail.
- Coût de la productivité réduite : les mouvements inutiles entraînent une productivité moindre.
Exemple : Coût total = (Temps perdu en heures) × (Salaire horaire) + (Coût des accidents ou arrêts) + (Coût de productivité réduite).
Surproduction :
- Coût des matières premières : la surproduction nécessite l’achat de plus de matières que nécessaire, immobilisant du capital.
- Coût de stockage : les produits en excès occupent de l'espace en entrepôt, augmentant ainsi les frais de stockage.
- Coût de dépréciation : les produits peuvent perdre de la valeur ou devenir obsolètes.
- Coût de destruction ou remise à niveau : en cas d'obsolescence, les
produits peuvent nécessiter une destruction, un recyclage ou engendrer un geste commerciale.
Exemple : Coût total = (Quantité de produits en excès) × (Coût unitaire) + (Coût de stockage par unité) + (Coût de dépréciation ou de remise commerciale).
Attentes :
- Coût des salaires : les employés sont rémunérés même lorsqu’ils attendent.
- Coût d’opportunité : l’entreprise perd de la capacité de production pendant ce temps.
- Coût d’immobilisation des équipements : machines et outils inutilisés
représentent une immobilisation de capital.
Exemple : Coût total = (Nombre d'heures d'attente) × (Salaire horaire) +
(Perte de production potentielle) + (Coût d'immobilisation des machines).
Surstokage et stocks inutiles :
- Coût de stockage : plus de stock nécessite plus d'espace, entraînant des frais de stockage supplémentaires (immobilisation d’espaces, frais d'énergie).
- Coût de détérioration ou d’obsolescence : les stocks peuvent se détériorer avec le temps ou devenir obsolètes.
- Coût du capital : l'argent investi dans des stocks excessifs ne peut pas être utilisé pour d'autres activités productives.
Exemple : Coût total = (Volume de stock excessif) × (Coût de stockage par unité) + (Coût d’obsolescence) + (Coût du capital immobilisé).
Transports :
- Coût du transport : frais de carburant, entretien des véhicules, usure des équipements de transport.
- Temps perdu : le temps passé à déplacer les matériaux aurait pu être utilisé pour la production.
- Risque de détérioration : les produits peuvent être endommagés pendant le transport, entraînant des coûts supplémentaires de réparation ou de remplacement.
Exemple : Coût total = (Distance parcourue inutilement) × (Coût de transport par km) + (Temps perdu en heures) × (Coût de main-d'œuvre) + (Coût des dommages potentiels).
Rebuts et retouches :
- Coût des matières premières perdues : les produits défectueux entraînent une perte de matières premières.
- Coût de la main-d’œuvre de reprise : temps et ressources supplémentaires pour réparer les défauts.
- Coût des retours clients : frais liés aux retours : remboursements ou réparations des produits vendus.
- Perte de réputation : une baisse de la qualité perçue peut entraîner une perte de clients ou de revenus futurs.
Exemple : Coût total = (Quantité de produits défectueux) × (Coût unitaire des matières) + (Temps de réparation) × (Coût horaire) + (Coût des retours et perte de réputation).
Étapes superflues :
- Coût des opérations superflues : certaines étapes du processus peuvent être coûteuses sans apporter de valeur ajoutée.
- Coût des machines et des équipements sous-utilisés : utilisation de machines complexes pour des tâches simples, entraînant des coûts d'amortissement élevés.
- Coût de non-qualité : les processus non adaptés peuvent entraîner une perte de qualité ou des défauts.
Exemple : Coût total = (Coût de chaque étape inutile) + (Amortissement des machines sous-utilisées) + (Coût de non-qualité).
Le rôle clé du contrôle de gestion
Il relie les mudas aux postes de coûts spécifiques, grâce à des règles de gestion dont il est le garant, en s’assurant que chaque gaspillage (surproduction, défauts, temps d’attente, ...) est correctement affecté aux coûts directs et indirects, qu’il soit ponctuel ou récurrent.
Cela inclut non seulement les coûts visibles comme les matières premières ou la main-d'œuvre, mais aussi des éléments moins tangibles comme l'immobilisation de trésorerie.
Le contrôle de gestion a également pour mission d'étudier les scénarios d'amélioration et de calculer le ROI (Retour sur Investissement) des actions de progrès, permettant de prioriser les initiatives.
En évaluant les gains potentiels et en créant des indicateurs clés de performance (KPI), il fournit une base solide pour évaluer l’efficacité des actions de progrès.
Enfin, le contrôle de gestion joue un rôle essentiel dans le suivi des indicateurs de performance et dans la validation des gains réalisés, actant ainsi que les efforts déployés se traduisent par des résultats tangibles.
La neutralité du contrôle de gestion maintient une position indépendante vis-à-vis des équipes dédiées à la démarche de progrès, assurant une analyse objective des performances et des gains obtenus.
Le blog de Lean en ligne - derniers articles publiés
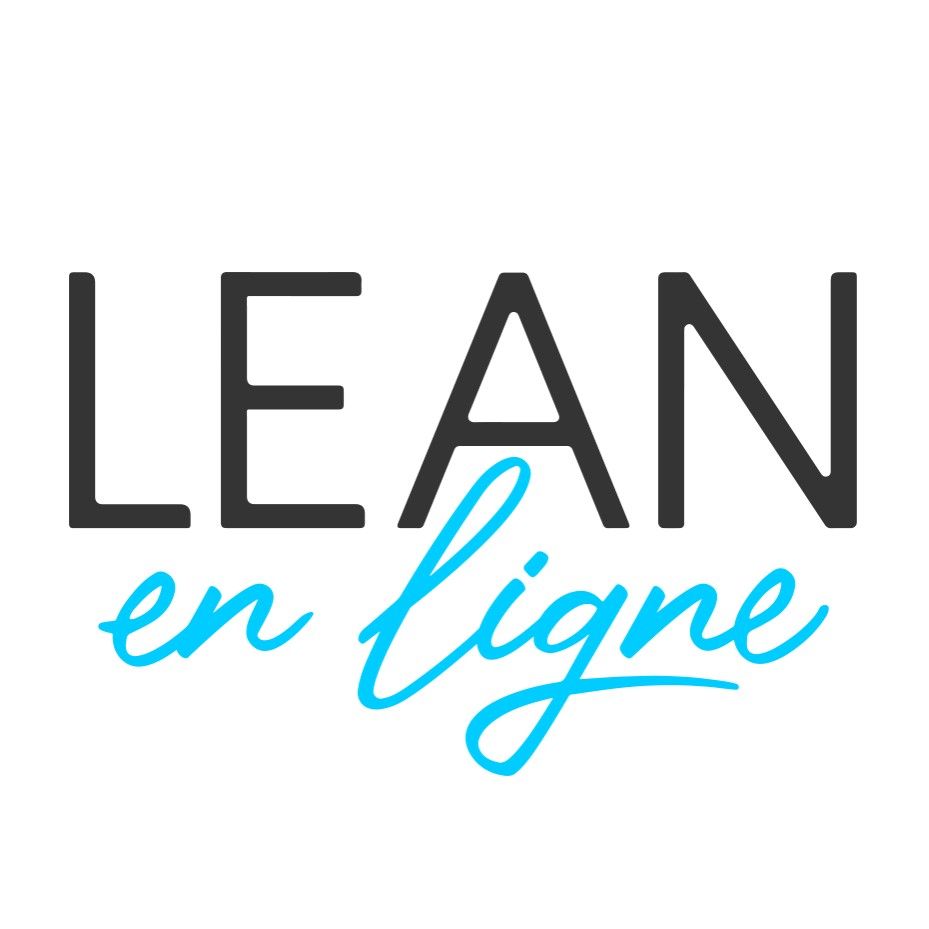
-
Lean en ligne - Sigmatic SAS
-
30 Boulevard de Sébastopol, 75004 Paris
-
+33 6 89 33 95 76
Nos offres
Formations à la une
Ressources gratuites
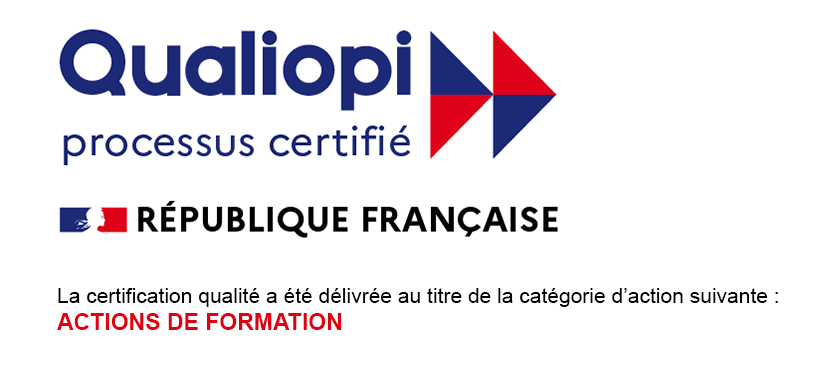