Comment rater le déploiement d'une démarche Lean ?
Oct 28
/
Damien Philippe
Le Lean Management, concept né dans les usines Toyota au Japon, est devenu une référence mondiale en matière d'amélioration continue et de gestion efficiente des processus. Toutefois, son déploiement à l'international, et plus particulièrement en France, présente des défis uniques.
Cet article explore l’histoire de l’expansion du Lean, les facteurs d’échec lors de son implémentation, ainsi que l'importance de la formation des collaborateurs pour assurer une transformation pérenne.
Cet article explore l’histoire de l’expansion du Lean, les facteurs d’échec lors de son implémentation, ainsi que l'importance de la formation des collaborateurs pour assurer une transformation pérenne.
Déploiement du Lean : quels bilans ?
Le Lean a pris son essor dans les années 1990, principalement après la publication de l'ouvrage "The Machine that Changed the World" qui a révélé les secrets de la production Toyota. Rapidement, des entreprises dans le monde entier ont cherché à adapter ces pratiques pour améliorer leur compétitivité.
Déploiement du Lean à l'international
Aux États-Unis, le Lean s'est imposé dans le secteur automobile avant de se propager à d'autres industries. Les entreprises américaines ont été parmi les premières à embrasser ces pratiques, motivées par des besoins de compétitivité face à l'industrie japonaise. En Europe, le Lean a aussi suscité un grand intérêt, mais son adaptation s'est faite plus progressivement, chaque pays ayant ses propres particularités culturelles et économiques.
- Secteur automobile. Le secteur automobile a été l’un des premiers à adopter le Lean en dehors du Japon. Aux États-Unis, des constructeurs tels que General Motors et Ford ont investi massivement dans l’adoption des principes du Toyota Production System (TPS). Ils ont cherché à réduire les stocks, à rationaliser les chaînes de production, et à diminuer les coûts opérationnels, tout en augmentant la qualité des produits. Le résultat a été une réduction notable des délais de production et une amélioration de la qualité, permettant aux constructeurs d'offrir des véhicules plus compétitifs.
- Secteur aéronautique. L’aéronautique a également rapidement adopté le Lean, notamment pour répondre aux exigences de qualité et de sécurité tout en réduisant les coûts et les délais de livraison. Airbus et Boeing, deux géants du secteur, ont intégré des principes Lean pour optimiser leurs chaînes d’approvisionnement, améliorer la gestion des pièces détachées, et diminuer les temps de cycle dans leurs ateliers. Les résultats dans ce secteur ont été impressionnants : Boeing a par exemple réduit de plusieurs semaines ses délais de production de certains avions, tout en améliorant les taux de conformité et de sécurité.
- Secteur manufacturier. Dans le secteur manufacturier, de nombreuses industries telles que l'électronique, la chimie ou encore le textile ont vu dans le Lean un moyen de rester compétitifs dans un environnement mondialisé et de plus en plus instable (voir notre article à propos de l'environnement VUCA). Dell, par exemple, a utilisé le Lean pour améliorer la gestion de ses stocks et réduire les gaspillages dans la production de ses ordinateurs. Grâce à l’application du Lean, Dell a pu diminuer le temps entre la commande et la livraison des ordinateurs tout en maintenant un faible niveau de stock, ce qui a contribué à sa domination dans les années 2000.
- Secteur logistique et distribution. Dans la logistique, le Lean a permis d’optimiser les flux et de minimiser les temps d’attente dans les entrepôts et lors des livraisons. Amazon, par exemple, utilise des principes Lean pour organiser ses centres de distribution, réduisant ainsi les délais de traitement des commandes et optimisant les livraisons. L'efficacité logistique obtenue grâce au Lean a été l'un des éléments clés de l'ascension rapide d'Amazon comme leader mondial du commerce en ligne.
- Secteur des services. Bien que le Lean soit souvent associé à l’industrie manufacturière, il a également trouvé un écho dans le secteur des services. Dans les banques et les assurances, le Lean est utilisé pour améliorer les processus internes, tels que le traitement des demandes de prêt ou de remboursement. Par exemple, plusieurs grandes banques américaines et européennes ont adopté le Lean pour réduire les délais de traitement des dossiers, améliorer l’expérience client et augmenter la productivité des équipes internes. Les résultats incluent une réduction des erreurs dans les dossiers et une augmentation de la satisfaction client.
Déploiement du Lean en France
En France, le Lean a souvent été perçu comme une méthode venue de l’étranger, et son adoption a rencontré plus de résistance. Les mentalités étaient ancrées dans une culture d’organisation rigide, avec un fort attachement à la hiérarchie et aux prérogatives décisionnelles. Néanmoins, certaines entreprises pionnières ont démontré les bénéfices du Lean, notamment dans les secteurs industriel et aéronautique.
L’un des défis majeurs en France a été l’implication des collaborateurs. Alors que le Lean prône l’autonomisation des équipes et la résolution de problèmes sur le terrain, beaucoup d’entreprises françaises ont eu du mal à encourager la prise d’initiatives chez les oprérationnels. De plus, l’accent mis sur la réduction des coûts a parfois été mal perçu, assimilé à une logique de réduction des effectifs (à tord ou à raison en fonction des cas).
L’un des défis majeurs en France a été l’implication des collaborateurs. Alors que le Lean prône l’autonomisation des équipes et la résolution de problèmes sur le terrain, beaucoup d’entreprises françaises ont eu du mal à encourager la prise d’initiatives chez les oprérationnels. De plus, l’accent mis sur la réduction des coûts a parfois été mal perçu, assimilé à une logique de réduction des effectifs (à tord ou à raison en fonction des cas).
- Secteur automobile français. Des entreprises comme Renault et PSA ont introduit le Lean dans leurs usines dès les années 2000. Confrontés à une concurrence croissante des constructeurs étrangers, ces groupes ont mis en place des chantiers Lean pour rationaliser leurs chaînes de montage et réduire les coûts de production. Par exemple, PSA a réduit de 30% le temps de production d’un véhicule en optimisant ses processus et en intégrant des pratiques de flux tendu. Ces améliorations ont contribué à améliorer la rentabilité du groupe, même en période de crise.
- Secteur aéronautique. Dans le secteur aéronautique français, Airbus a été un leader dans l'adoption du Lean, notamment dans ses usines de Toulouse. En intégrant des pratiques Lean comme la méthode 5S, Airbus a pu optimiser l'assemblage de ses avions, réduisant les temps de cycle et améliorant la qualité des composants. L'optimisation des processus a contribué à une hausse de la productivité de 20% sur certaines lignes de production et à une réduction des coûts de maintenance.
- Secteur hospitalier. Le secteur de la santé, bien que traditionnellement éloigné des pratiques industrielles, a commencé à intégrer le Lean dans la gestion des hôpitaux et des services médicaux. Certains hôpitaux français, comme le CHU de Grenoble, ont introduit le Lean pour améliorer la gestion des urgences, réduire les temps d'attente, et optimiser l'utilisation des équipements médicaux. Les résultats ont été notables, avec une réduction significative des délais d'attente des patients et une meilleure gestion des ressources.
- Secteur agroalimentaire. Dans l’industrie agroalimentaire, des entreprises comme Danone ont utilisé les principes Lean pour optimiser leurs lignes de production et améliorer la qualité des produits. En appliquant des méthodes de réduction des gaspillages et en formant leurs équipes à l'amélioration continue, Danone a réussi à réduire de 15% les pertes en production, tout en maintenant des standards de qualité très élevés.
Comment rater le déploiement du Lean ?
Déployer une démarche de progrès n'est pas sans difficulté. Voici quelques-uns des facteurs d'échec les plus souvent rencontrés :
Un manque d'engagement du top management. L'un des principaux facteurs d'échec du Lean réside dans le manque d'engagement de la Direction. Le Lean nécessite un changement culturel profond, impliquant tous les niveaux de l'organisation, à commencer par le sommet. Si les dirigeants ne sont pas activement engagés et convaincus des bénéfices à long terme du Lean, il est très probable que l’initiative échoue. Certaines entreprises décident de déployer le Lean pour "faire comme tout le monde", sans une réelle volonté de transformation. Les dirigeants attendent des résultats immédiats mais ne consacrent pas le temps, les ressources et le leadership nécessaires pour réussir. Sans l’implication directe de la Direction, les équipes se démotivent, les projets Lean stagnent et la démarche s’essouffle rapidement. Voir notre article de blog intitulé "Pourquoi déployer le Lean".
L'absence de vision à long terme. Le Lean est un marathon, pas un sprint. Certaines entreprises veulent des résultats immédiats et abandonnent lorsque les gains rapides (quick win) ne sont pas visibles. Une vision claire et un plan à long terme sont indispensables pour assurer le caractère pérenne des transformations. Par exemple, une entreprise peut tenter de réduire ses effectifs pour améliorer temporairement sa rentabilité, mais ce type d'approche contradictoire avec l’esprit Lean se traduit souvent par une surcharge de travail pour les équipes restantes et une diminution de la qualité.
Une sous-estimation des enjeux de conduite du changement. Le Lean implique un changement radical dans la manière dont les processus sont gérés et dans l’implication des collaborateurs. Ce bouleversement est souvent accueilli avec une certaine résistance, surtout dans des environnements où les méthodes traditionnelles sont profondément ancrées. Le Lean peut être perçu comme une menace par les employés, en particulier lorsque les finalités de la démarche ne sont pas expliquées. Si les équipes considèrent que l'initiative Lean se résume à des coupes budgétaires ou à des suppressions de postes, elles risquent de développer une résistance passive ou active. Pour contourner cet écueil, il est essentiel de mettre en place un programme de communication claire et de montrer que le Lean est une opportunité d’amélioration pour tous, et non un outil de réduction d’effectifs.
Un déploiement fragmenté. Certaines entreprises tentent d’adopter uniquement certaines pratiques Lean sans en saisir l’esprit global. L'absence de cohérence et l'implantation de processus sans une compréhension profonde du Lean mènent souvent à des résultats médiocres. Nous vous suggérons à ce titre de lire notre article à propos du But qui explique les fondements de la théorie des contraintes.
Un manque d'engagement du top management. L'un des principaux facteurs d'échec du Lean réside dans le manque d'engagement de la Direction. Le Lean nécessite un changement culturel profond, impliquant tous les niveaux de l'organisation, à commencer par le sommet. Si les dirigeants ne sont pas activement engagés et convaincus des bénéfices à long terme du Lean, il est très probable que l’initiative échoue. Certaines entreprises décident de déployer le Lean pour "faire comme tout le monde", sans une réelle volonté de transformation. Les dirigeants attendent des résultats immédiats mais ne consacrent pas le temps, les ressources et le leadership nécessaires pour réussir. Sans l’implication directe de la Direction, les équipes se démotivent, les projets Lean stagnent et la démarche s’essouffle rapidement. Voir notre article de blog intitulé "Pourquoi déployer le Lean".
L'absence de vision à long terme. Le Lean est un marathon, pas un sprint. Certaines entreprises veulent des résultats immédiats et abandonnent lorsque les gains rapides (quick win) ne sont pas visibles. Une vision claire et un plan à long terme sont indispensables pour assurer le caractère pérenne des transformations. Par exemple, une entreprise peut tenter de réduire ses effectifs pour améliorer temporairement sa rentabilité, mais ce type d'approche contradictoire avec l’esprit Lean se traduit souvent par une surcharge de travail pour les équipes restantes et une diminution de la qualité.
Une sous-estimation des enjeux de conduite du changement. Le Lean implique un changement radical dans la manière dont les processus sont gérés et dans l’implication des collaborateurs. Ce bouleversement est souvent accueilli avec une certaine résistance, surtout dans des environnements où les méthodes traditionnelles sont profondément ancrées. Le Lean peut être perçu comme une menace par les employés, en particulier lorsque les finalités de la démarche ne sont pas expliquées. Si les équipes considèrent que l'initiative Lean se résume à des coupes budgétaires ou à des suppressions de postes, elles risquent de développer une résistance passive ou active. Pour contourner cet écueil, il est essentiel de mettre en place un programme de communication claire et de montrer que le Lean est une opportunité d’amélioration pour tous, et non un outil de réduction d’effectifs.
Un déploiement fragmenté. Certaines entreprises tentent d’adopter uniquement certaines pratiques Lean sans en saisir l’esprit global. L'absence de cohérence et l'implantation de processus sans une compréhension profonde du Lean mènent souvent à des résultats médiocres. Nous vous suggérons à ce titre de lire notre article à propos du But qui explique les fondements de la théorie des contraintes.
Une confusion entre Lean et cost-killing. Le Lean vise à créer de la valeur tout en éliminant les gaspillages. Il ne s’agit pas simplement de réduire les coûts. Trop d’entreprises tombent dans le piège de voir le Lean uniquement comme une méthode pour "faire plus avec moins", en réduisant les ressources sans penser à la qualité ou à l'efficacité globale. Une entreprise qui réduit drastiquement ses effectifs sous couvert de Lean sans optimiser les processus et sans garantir la satisfaction des clients verra très probablement une dégradation de la qualité et une augmentation des erreurs, ce qui impactera négativement ses résultats à long terme.
Un manque de personnalisation du Lean aux spécificités de l’entreprise. Le Lean n'est pas une solution universelle qui s'applique de manière identique dans toutes les organisations. Il doit être adapté aux spécificités de chaque entreprise, que ce soit en termes de culture, de processus, ou d'objectifs stratégiques.
Certaines entreprises du secteur tertiaire tentent d’adopter des outils Lean conçus pour l’industrie manufacturière sans les ajuster à leur réalité opérationnelle. Cela mène à une mauvaise adoption et à des résultats décevants.
Ne pas embarquer l’ensemble de l’entreprise. Le Lean ne concerne pas uniquement les équipes de production ou les services techniques. Il doit être intégré dans tous les départements de l’entreprise : finance, marketing, ressources humaines, etc. Si une organisation ne l'applique que dans certains services et ignore les autres, elle rate l’occasion d’obtenir des gains transversaux. Certaines entreprises se concentrent uniquement sur l’amélioration des processus de production tout en négligeant les départements comme les ressources humaines ou les ventes, ce qui empêche de diffuser une culture d’amélioration continue à l’échelle de l’organisation de manière transverse.
L'absence de suivi des résultats et d’ajustement. Une démarche Lean ne peut pas être considérée comme un projet unique à réaliser puis à clôturer. Il s'agit d'une approche qui nécessite un suivi constant des résultats, des ajustements réguliers, et un retour d’expérience pour s'améliorer en permanence. Certaines entreprises lancent des projets d'amélioration, mais ne mesurent pas les gains obtenus ni les éventuels problèmes qui peuvent survenir. Sans suivi, il n'est pas possible d'évaluer l'impact de la démarche sur l'organisation. Nous vous recommandons sur le sujet, le replay de webinaire "L'importance de la mesure".
Un manque de formation et de mise en pratique. Cet axe sera développé dans le paragraphe suivant.
Un manque de formation et de mise en pratique. Cet axe sera développé dans le paragraphe suivant.
Formation et pratique : clés d'un déploiement Lean
Le succès du déploiement Lean repose sur deux piliers essentiels : la formation des collaborateurs et la mise en pratique régulière des concepts Lean. Si la formation est indispensable pour acquérir les compétences et l’état d’esprit nécessaire, c’est la pratique qui permet de transformer les connaissances théoriques en résultats concrets et durables.
Formation : préparer les collaborateurs à la Transformation
Les enjeux liés à la formation sont multiples :
Acquérir les connaissances fondamentales et les outils Lean
Le Lean Management repose sur des outils et des concepts précis, tels que le Kaizen, la cartographie des processus, le Kanban, la méthode 5S ou encore la standardisation. Une formation adéquate permet aux collaborateurs d'acquérir les connaissances théoriques nécessaires pour comprendre ces outils et les appliquer efficacement. Cela consiste à familiariser les collaborateurs avec les termes techniques et les méthodologies propres au Lean. Transmettre les bonnes pratiques pour identifier les gaspillages (Muda) et améliorer la chaîne de valeur. S’assurer que les équipes comprennent que le Lean est une démarche holistique, allant bien au-delà de simples outils pour devenir un véritable état d’esprit. Voir notre formation White Belt.
Changer les mentalités et développer l’état d’esprit Lean
L’un des défis majeurs de toute transformation Lean est le changement de mentalité. Le Lean encourage une remise en question constante des pratiques établies, avec une focalisation sur la création de valeur pour le client et l’élimination des gaspillages. Pour cela, il est essentiel de former les collaborateurs non seulement aux outils, mais aussi à l’état d’esprit Lean. Promouvoir une culture de l'amélioration continue, où chaque collaborateur, quel que soit son niveau, se sent responsable de proposer des améliorations.
Développer une approche centrée sur la résolution de problèmes, où les erreurs ne sont pas sanctionnées (challenger des processus et non des individus), mais considérées comme des opportunités d’apprentissage.
Inculquer le principe du respect des personnes, fondement du Lean, en responsabilisant les équipes et en valorisant leurs idées.
Former à tous les niveaux de l’organisation
Le Lean n’est efficace que si l’ensemble de l’entreprise est impliqué, de la Direction aux équipes opérationnelles. Chaque niveau de l’organisation doit suivre une formation adaptée à son rôle.
Certification et progression des compétences
Le Lean offre des programmes de formation certifiants, qui permettent de structurer les niveaux de compétence dans l’entreprise, avec des certifications telles que White Belt, Yellow Belt, Green Belt, et Black Belt. Cela permet d'instaurer un parcours de montée en compétences pour les collaborateurs, de créer une équipe de champions Lean certifiés, capables de piloter les projets Lean et de diffuser la culture d'amélioration continue dans toute l'organisation et de garantir que chaque collaborateur, à son niveau, dispose des compétences nécessaires pour contribuer à la démarche.
Acquérir les connaissances fondamentales et les outils Lean
Le Lean Management repose sur des outils et des concepts précis, tels que le Kaizen, la cartographie des processus, le Kanban, la méthode 5S ou encore la standardisation. Une formation adéquate permet aux collaborateurs d'acquérir les connaissances théoriques nécessaires pour comprendre ces outils et les appliquer efficacement. Cela consiste à familiariser les collaborateurs avec les termes techniques et les méthodologies propres au Lean. Transmettre les bonnes pratiques pour identifier les gaspillages (Muda) et améliorer la chaîne de valeur. S’assurer que les équipes comprennent que le Lean est une démarche holistique, allant bien au-delà de simples outils pour devenir un véritable état d’esprit. Voir notre formation White Belt.
Changer les mentalités et développer l’état d’esprit Lean
L’un des défis majeurs de toute transformation Lean est le changement de mentalité. Le Lean encourage une remise en question constante des pratiques établies, avec une focalisation sur la création de valeur pour le client et l’élimination des gaspillages. Pour cela, il est essentiel de former les collaborateurs non seulement aux outils, mais aussi à l’état d’esprit Lean. Promouvoir une culture de l'amélioration continue, où chaque collaborateur, quel que soit son niveau, se sent responsable de proposer des améliorations.
Développer une approche centrée sur la résolution de problèmes, où les erreurs ne sont pas sanctionnées (challenger des processus et non des individus), mais considérées comme des opportunités d’apprentissage.
Inculquer le principe du respect des personnes, fondement du Lean, en responsabilisant les équipes et en valorisant leurs idées.
Former à tous les niveaux de l’organisation
Le Lean n’est efficace que si l’ensemble de l’entreprise est impliqué, de la Direction aux équipes opérationnelles. Chaque niveau de l’organisation doit suivre une formation adaptée à son rôle.
- Pour les dirigeants, il s'agit d'acquérir une vision stratégique du Lean et comprendre comment aligner les objectifs Lean avec les objectifs financiers et opérationnels de l’entreprise. Les dirigeants doivent comprendre les enjeux associés au rôle de Sponsor dans les projets d'amélioration.
- Pour les managers : apprendre à coacher leurs équipes, encourager l'autonomie et à suivre les résultats Lean sans imposer des solutions top-down (voir notre article à propos de l'innovation participative)
-
Pour les opérationnels : comprendre comment les outils Lean peuvent améliorer leur quotidien, réduire les gaspillages et améliorer leurs conditions de travail.
Certification et progression des compétences
Le Lean offre des programmes de formation certifiants, qui permettent de structurer les niveaux de compétence dans l’entreprise, avec des certifications telles que White Belt, Yellow Belt, Green Belt, et Black Belt. Cela permet d'instaurer un parcours de montée en compétences pour les collaborateurs, de créer une équipe de champions Lean certifiés, capables de piloter les projets Lean et de diffuser la culture d'amélioration continue dans toute l'organisation et de garantir que chaque collaborateur, à son niveau, dispose des compétences nécessaires pour contribuer à la démarche.
Pratique : transformer les principes et les concept en résultats concrets
Les enjeux liés à la pratique sont multiples :
Ancrer le Lean dans les pratiques quotidiennes grâce aux rituels
Une fois la formation théorique acquise, le défi est de mettre en pratique les enseignements dans le quotidien de l’entreprise. Le Lean ne peut être un succès que s'il est ancré dans les comportements de tous les jours. Les rituels de performance sont des outils essentiels pour faciliter cette mise en pratique (voir notre article à propos de la démarche QRQC). Les réunions quotidiennes permettent aux équipes de suivre la performance et de résoudre les problèmes.
Maintenir un suivi régulier des performances, des améliorations en cours et des éventuels obstacles rencontrés. Créer une dynamique d’équipe où chaque collaborateur est impliqué dans la résolution de problèmes. Instaurer des cycles d’amélioration continue à travers des revues régulières des résultats, comme le Kaizen et le PDCA (Plan Do Check Act).
L’application des outils Lean sur le terrain
La formation seule ne suffit pas à faire du Lean une réussite. Les équipes doivent être encouragées à appliquer les outils qu’elles ont appris dans des situations réelles, sur le terrain. Cela peut inclure l’utilisation de la cartographie des flux de valeur pour identifier les gaspillages, ou la mise en place du système Kanban pour améliorer la gestion des stocks. Accompagner les collaborateurs dans la mise en pratique des outils Lean pour éviter qu’ils ne se limitent à une approche théorique. Impliquer les managers dans des gemba walks (visites sur le terrain), afin de s’assurer que les équipes appliquent correctement les concepts Lean et d’identifier directement les opportunités d’amélioration.
Mesurer les résultats des initiatives Lean en temps réel, avec des indicateurs clés de performance (KPI) adaptés.
Promouvoir une culture de la transparence et du feedback
La pratique du Lean nécessite une culture forte de la transparence, où chaque problème est vu comme une opportunité d’amélioration. Les collaborateurs doivent se sentir en confiance pour signaler les dysfonctionnements sans craindre de répercussions. Cela est particulièrement important dans un contexte Lean, où la résolution de problèmes est au cœur du processus. Encourager une remontée d’information fluide pour identifier les goulots d’étranglement ou les gaspillages dans les processus.
Développer une culture du feedback constructif, où les managers et les équipes échangent régulièrement sur les réussites et les axes d’amélioration. Instaurer une démarche de "no blame" (pas de reproches), où les erreurs sont considérées comme des occasions d’apprentissage et non des échecs.
Construire une entreprise apprenante
Un des objectifs du Lean est de transformer l’organisation en entreprise apprenante, où chaque collaborateur apprend en permanence de ses expériences et des résultats obtenus. Pour cela, il est crucial de créer un environnement où la pratique du Lean devient naturelle et où les rituels d’amélioration sont ancrés dans le quotidien. Créer des cycles continus d’apprentissage à travers des pratiques comme les revues Kaizen, qui permettent aux équipes d’évaluer régulièrement leurs processus et de proposer des améliorations. Mettre en place des systèmes de partage de connaissances, pour que les bonnes pratiques découvertes dans un département puissent être diffusées à l’ensemble de l’organisation.
Assurer que l’ensemble de l’entreprise s’inscrive dans une logique d’amélioration continue, où chaque collaborateur se sent à la fois acteur et bénéficiaire des transformations.
Ancrer le Lean dans les pratiques quotidiennes grâce aux rituels
Une fois la formation théorique acquise, le défi est de mettre en pratique les enseignements dans le quotidien de l’entreprise. Le Lean ne peut être un succès que s'il est ancré dans les comportements de tous les jours. Les rituels de performance sont des outils essentiels pour faciliter cette mise en pratique (voir notre article à propos de la démarche QRQC). Les réunions quotidiennes permettent aux équipes de suivre la performance et de résoudre les problèmes.
Maintenir un suivi régulier des performances, des améliorations en cours et des éventuels obstacles rencontrés. Créer une dynamique d’équipe où chaque collaborateur est impliqué dans la résolution de problèmes. Instaurer des cycles d’amélioration continue à travers des revues régulières des résultats, comme le Kaizen et le PDCA (Plan Do Check Act).
L’application des outils Lean sur le terrain
La formation seule ne suffit pas à faire du Lean une réussite. Les équipes doivent être encouragées à appliquer les outils qu’elles ont appris dans des situations réelles, sur le terrain. Cela peut inclure l’utilisation de la cartographie des flux de valeur pour identifier les gaspillages, ou la mise en place du système Kanban pour améliorer la gestion des stocks. Accompagner les collaborateurs dans la mise en pratique des outils Lean pour éviter qu’ils ne se limitent à une approche théorique. Impliquer les managers dans des gemba walks (visites sur le terrain), afin de s’assurer que les équipes appliquent correctement les concepts Lean et d’identifier directement les opportunités d’amélioration.
Mesurer les résultats des initiatives Lean en temps réel, avec des indicateurs clés de performance (KPI) adaptés.
Promouvoir une culture de la transparence et du feedback
La pratique du Lean nécessite une culture forte de la transparence, où chaque problème est vu comme une opportunité d’amélioration. Les collaborateurs doivent se sentir en confiance pour signaler les dysfonctionnements sans craindre de répercussions. Cela est particulièrement important dans un contexte Lean, où la résolution de problèmes est au cœur du processus. Encourager une remontée d’information fluide pour identifier les goulots d’étranglement ou les gaspillages dans les processus.
Développer une culture du feedback constructif, où les managers et les équipes échangent régulièrement sur les réussites et les axes d’amélioration. Instaurer une démarche de "no blame" (pas de reproches), où les erreurs sont considérées comme des occasions d’apprentissage et non des échecs.
Construire une entreprise apprenante
Un des objectifs du Lean est de transformer l’organisation en entreprise apprenante, où chaque collaborateur apprend en permanence de ses expériences et des résultats obtenus. Pour cela, il est crucial de créer un environnement où la pratique du Lean devient naturelle et où les rituels d’amélioration sont ancrés dans le quotidien. Créer des cycles continus d’apprentissage à travers des pratiques comme les revues Kaizen, qui permettent aux équipes d’évaluer régulièrement leurs processus et de proposer des améliorations. Mettre en place des systèmes de partage de connaissances, pour que les bonnes pratiques découvertes dans un département puissent être diffusées à l’ensemble de l’organisation.
Assurer que l’ensemble de l’entreprise s’inscrive dans une logique d’amélioration continue, où chaque collaborateur se sent à la fois acteur et bénéficiaire des transformations.
Vous avez apprécié cet article ? Faites-le savoir !
Le blog de Lean en ligne - derniers articles publiés
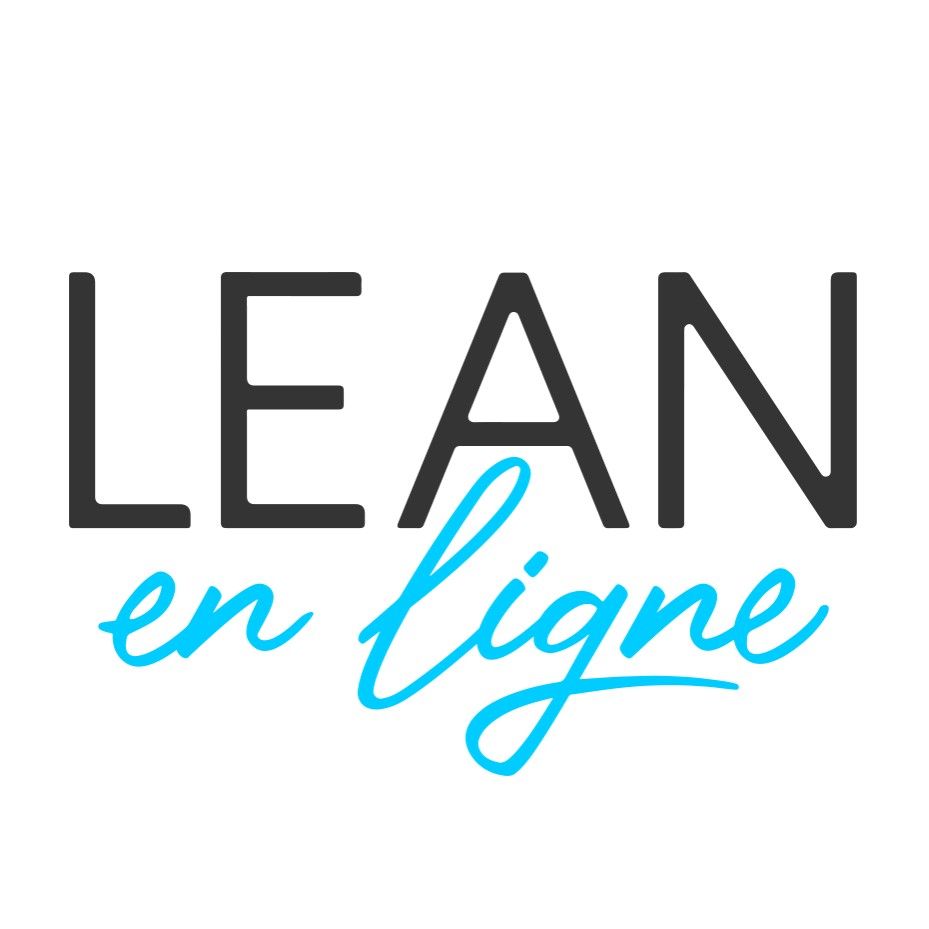
-
Lean en ligne - Sigmatic SAS
-
30 Boulevard de Sébastopol, 75004 Paris
-
+33 6 89 33 95 76
Suivre l'actualité de Lean en ligne
Merci et à bientôt !
Nos offres
Formations à la une
Ressources gratuites
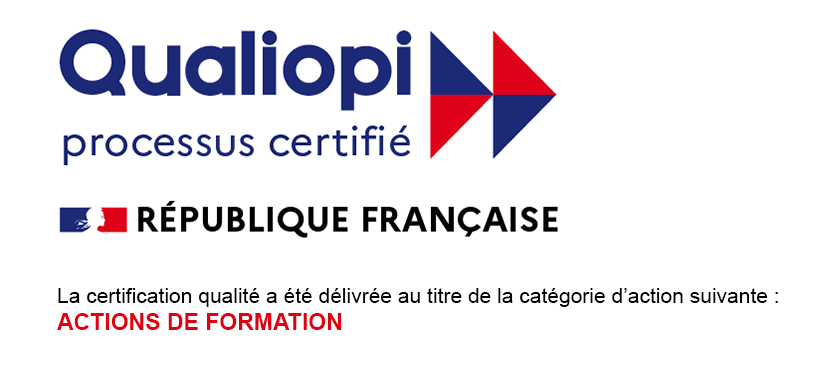
Organisme de Formation enregistré sous le numéro 11756146475. Cet enregistrement ne vaut pas agrément de l’État
Write your awesome label here.
On reste en contact ?
Merci à bientôt !